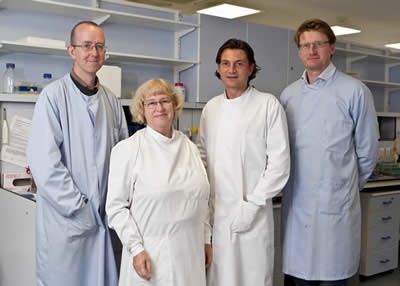
Student: Dr Chris Cherry
Company: MicroPharm Ltd
Academic Supervisor: Dr Huw Millward (PDR) and Prof. Rose Cooper (CSHS)
Cardiff Metropolitan University has recently had its first KESS PhD completion; the project developed novel packaging solutions for the freeze-drying of specialist pharmaceuticals. The KESS student, Dr Chris Cherry, was based at the host company, MicroPharm Ltd in West Wales. The academic supervision for the project was provided jointly by The National Centre for Product Design & Development Research (PDR) and The Cardiff School of Health Sciences (CSHS); both academic schools are based on Cardiff Met’s Llandaff Campus. The KESS project covered the science of mass and heat transfer characterisation through to the challenges of maintaining sterility and containment within a freeze dryer. This research project delivered a very successful PhD in just over three years. In addition, the collaborative nature of the project has derived a range of supplementary benefits for the student, company and university. This case study describes the chronology of the KESS project, and attempts to capture the tangible (and intangible) benefits to the three main parties.
A successful KESS project needs the right problem to solve, a diligent student and a good working relationship between the university and company partners. In this case, the partnership between Cardiff Met and MicroPharm had started some years before the KESS award. Darragh Murphy (Research Officer at PDR) led the Winnovate project, an EU-funded Interreg IIIA programme to enhance the product development capability of SMEs in rural West Wales. Prof. John Landon (chairman of MicroPharm) joined the programme, and engaged with PDR for support on a number of design and development issues. MicroPharm is based in Newcastle Emlyn, and has 25 staff. The company specialises in the development and manufacture of ovine antisera containing high densities of specific antibodies. MicroPharm’s core expertise is the purification and modification of these antibodies to produce an extensive range of immunotherapeutic products for clinical use. The ovine-derived immunotherapies are targeted to treat acute, life-threatening emergencies, such as anti-venom for the treatment of snake bites in West Africa. A typical anti-venom product requires freeze-drying to keep it stable and active in the absence of a refrigerated cold-chain. Although anti-venom products are urgently required by medical professionals, they are small batch sizes, and therefore are uneconomic to produce using conventional sterile manufacturing facilities.
Prof. Landon was keen to develop alternative freeze-drying processes that would allow the sterile freeze-drying of products within an ‘unclean’ conventional laboratory environment; as opposed to the time and expense of relocating complex freeze-drying equipment to a specialist clean room. Other research establishments had attempted to develop containment solutions for sterile freeze-drying but they had failed. Consequently, there was a clear practical need for this work but it would need the time and rigour associated with a three-year PhD study. PDR and MicroPharm discussed the available options and it was clear that a KESS PhD was the ideal vehicle to deliver the required knowledge. Prof. Landon quickly identified the KESS student (Chris Cherry), and the academic supervision was provided jointly by Dr Huw Millward (PDR) and Prof. Rose Cooper (CSHS). Following the funding application and formal selection process, the KESS project started on 1st March 2010.
Freeze-drying is an inherently complex process involving the sublimation of water from the solid phase (ice) direct to the vapour phase. Water is the solvent of life; therefore the removal of water to produce a powdered pharmaceutical product prevents the growth of microorganisms and maintains the stability of key biological material. In biopharmaceutical freeze-drying, the product (in its initial aqueous solution) is frozen at a very low temperature,
and a vacuum applied to initiate sublimation of the water. This primary freeze-drying phase is characterised by the loss of water coupled with heat input to control the rate of sublimation. The secondary freeze-drying phase then applies gentle heat to remove the remaining water and leave a residual moisture level of around 1%. The resulting dry powder matrix is a complex porous structure, ideally containing biologically material that is still active and viable for clinical use.
Given the complex nature of freeze-drying, the aim of the first year of the PhD was to build up a detailed knowledge of the area through literature review, pilot-scale experimentation and the development of appropriate test methods and techniques. The KESS budget for Equipment & Consumables and Travel & Conference expenses was put to good use during the first year. Chris Cherry sourced and commissioned an appropriate freeze-dryer, and this allowed the base-line freeze-drying cycles to be established. The leading freeze-drying researchers in the UK were identified, and the KESS student travelled to Aston University and The National Institute for Biological Standards and Control to gain access to state-of-the-art analytical equipment. In September 2010 the largest worldwide meeting of freeze-drying experts was held in the ski resort of Garmisch-Partenkirchen, Germany. Chris Cherry attended the training events and two-day conference, and this proved an ideal opportunity to meet leading international researchers and get early guidance on the PhD project. At the end of year one, Chris Cherry’s work on model protein development and optimum freeze-drying cycles was written up as a Transfer Report, and this allowed progression to full PhD status.
The academic grounding for the PhD was established during year one of the KESS project; at the start of year two, a commercial perspective was sought. Biopharma Ltd provides freeze-drying products and associated consultancy services throughout Europe, and they were invited to Cardiff Met to review the containment concepts under development. A range of designs for freeze-drying containment were presented, and a lead concept was quickly identified, namely disposable sterilisation pouches. This concept was selected on the basis that sterilisation pouches are an economically-viable solution for SMEs operating in this field. The key data collection phase of the PhD then started. Fully-calibrated pressure and temperature gauges were integrated into the freeze-drying equipment, and this enabled the mass transfer and heat transfer properties of the novel containment pouches to be fully characterised. This piece of research was the first to demonstrate that freeze-drying was technically feasible using disposable pouches, plus the new containment approach did not disrupt delicate pharmaceutical formulations (i.e. the powdered end-product was still clinically viable).
The final phase of experimental work at the start of the third year needed to show that the disposable pouches could maintain sterility within the pouch (no microbial ingress) and also maintain containment (prevent powdered egress), whilst still allowing the freeze-drying process to occur. At this stage of the PhD, Chris Cherry had developed in-depth knowledge of the freeze-drying process and could configure a complete collapse of the dry-layer product or ablation (explosive release) of the powder. The containment systems were challenged with aerosolised microbial cells and no ingress was measured within the pouches. Crucially, ablated microbial cells were successfully contained within the pouches, thus preventing contamination of the freeze-dryer environment. The completion of all experimental work triggered two key academic publications. In August 2012, a poster was presented at the biennial freeze-drying conference in Colorado, USA. The feedback from discussions with world-leading researchers then informed a peer-reviewed journal paper: ‘A novel approach to sterile pharmaceutical freeze drying’. The paper was published in January
2013 in Pharmaceutical Development and Technology. The journal publication was an important milestone in the PhD – it provided external validation of the research findings. The KESS student then spent the final four months of the KESS project writing up his PhD thesis, which was submitted in April 2013. The candidate gave a strong defence of his work at the viva voce examination in June 2013, and the PhD degree was awarded following minor corrections.
The KESS programme has enabled the three partners (student, company and university) to progress a piece of research from a vague, early-stage concept through to a successful PhD completion. Naturally, the KESS student is the key facilitator in this process. Skills development in this case enabled Chris Cherry to build up a detailed knowledge of freeze-drying over a logical series of stages: academic literature, engagement with UK experts and training/conference events with world-leading researchers. Dr Cherry developed research methods in the areas of analytical chemistry, biochemical engineering and microbial-challenge techniques. In addition, he presented his research both locally and internationally, and developed an academic writing style that was appropriate for peer-reviewed journals and the final PhD thesis. This skill set was immediately transferable to the commercial environment, and Chris Cherry was appointed Pharmaceutical Production Manager at MicroPharm. His new industrial position has not stopped the freeze-drying research – follow on publications and collaborative projects are currently being explored.
MicroPharm Ltd is not a typical SME; they are a forward-thinking company, not afraid of long-term research and are ready to engage with academic partners to develop new knowledge. The KESS project was an ideal vehicle for staff development in tandem with providing a solution to a practical production problem. The containment pouches developed through the project are elegant and inexpensive, and have the potential to make a significant positive impact on companies, such as MicroPharm, who are developing niche pharmaceutical products for rare diseases. In addition, MicroPharm has engaged with a number of the UK’s leading freeze-drying organisations and these relationships have allowed the company to offer their contract manufacturing capability to a new cohort of customers. The KESS project has had an immediate effect on the services offered by the company, while the PhD provides a solid foundation to any longer-term new product development in the area of freeze-drying.
The clear advantage of KESS over other knowledge transfer programmes is that activities are focused on one key deliverable: a successful PhD completion. This PhD journey has brought a range of benefits to Cardiff Metropolitan University. The project has strengthened collaboration within the university, specifically between PDR and CSHS. The research staff had some experience of freeze-drying prior to the start of the project, but the research has provided significant new insights into this under-researched area. This, in turn, has allowed Cardiff Met to explore other freeze-drying projects in partnership with Welsh industry. The peer-reviewed publication resulting from the PhD has been rated internationally excellent in terms of originality, significance and rigour, and will be submitted in the 2014 Research Excellence Framework. This freeze-drying project has also facilitated a second KESS award between CSHS and MicroPharm – the second project is developing new techniques for infection control. The KESS programme overall has made a positive impact on the research staff at Cardiff Met, and the university would be very keen to support a second phase of funding for KESS PhD projects.